Role of motor controllers in EVs and why India has been relying on imports
Electric mobility is rapidly replacing the conventional ICE based power trains used in vehicles. Electric power trains are more efficient and environmental friendly. The performance and efficiency of electric power trains are achieved by advanced motors and motor controllers. Most of the electric power trains that we know today uses BLDCM (Brush Less Direct Current Motor) or PMSM (Permanent Magnet Synchronous Motor). These Motors are very light and efficient compared to the conventional motors, and for these motors to function, a motor controller is essential.
Purpose of a motor controller in an EV
Motor controller is a combination of Power electronics and embedded micro-computing elements which make the efficient conversion of energy stored in batteries of an electric vehicle to generate motion.
The cover image shows a simplified block diagram of commonly used electric 3 wheeler vehicle.
As one can see, motor controller acts as the major component which controls the energy flow to the motor. Interfaces like Throttle, Brake or Forward/Reverse control switches are connected to the Motor controller, which processes the commands from these inputs and very precisely controls the speed, torque, direction, and resulting horsepower of a motor in the vehicle.
Apart from transferring the energy from battery to motor for generating acceleration for the vehicle, Motor controllers also can reverse the energy from Motor back to batteries which helps the electric vehicles to brake more effectively than a simple mechanical brake system. This capability commonly known as “Regenerative Braking” also helps the electric vehicle to improve its range by storing energy back in batteries at each instance of braking.
Parts of a motor controller
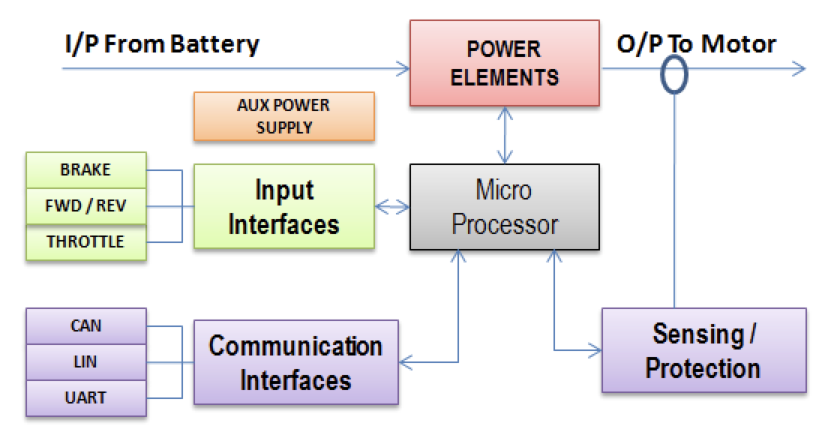
The heart of the system is a micro processor which has an embedded firmware to realize all the functionalities of the Motor controller.
Power elements block is the power electronics portion which is basically a bi- directional power converter. It has the capability to transfer energy from battery to motor and vice versa.
Input interface block helps to connect the other vehicle electronics and interfaces to the motor controller.
Sensing/protection block measures all parameters of the system like battery voltage, current, motor speed, voltage, current etc. All these parameters are closely monitored and precisely controlled by the motor controller. Any fault detected in the system will trigger self protection ensuring the vehicle and passenger safety.
Communication block is one of the most important parts of the motor controller unit as it enables the motor controller to share the data with external systems. Motor controller can send data and receive commands through communication block. Future of the mobility is moving towards shared and autonomous vehicles. The capability to share the data and synchronise with external systems in real time makes a motor controller and an electric power train a better candidate for enabling shared and autonomous mobility.
Why making the controllers has been a challenge in India
It is common knowledge that a vast majority of motor controllers used in India are imported. Following are challenges with making controllers in India.
– It should be noted that motor companies in India have been traditionally manufacturing induction motors and Brushed DC motors which DO NOT need controllers. BLDC motors have only recently been introduced for different application areas such as EVs, as well as inverters technology for air conditioners and refrigerators. So, we can say the requirement of controllers in the market is relatively new.
– Lack of technical capability at organisational level and individual skill level is another reason. Notably, manufacturing of motor controllers need multi-disciplinary proficiency in embedded systems, power electronics, control systems and electrical machines. There is a lack of curriculum and practical opportunities to help individuals develop these skills.
– Semi conductor devices are a basic component of a motor controller. Though these are not manufactured in India, there is still a decent supply chain already available that imports semi conductors and supplies the same to Indian companies. The main challenge with manufacturing of controllers is with the process required to build controllers that can withstand high amounts of current.
Light EVs in India predominantly use the low voltage 48V electrical systems. While these systems have the advantage of low safety risks, it leads to high current (up to 250 Amps) to deliver high level of vehicle performance. Manufacturing controllers that can handle such high current needs complex processes that come with their own challenges.
At, C Electric – we work along with our local electronic manufacturing partners to attach copper components to PCBs. While the PCB performs the basic functions of the controller, the copper elements help handle higher amount of current. The integration of copper components with the PCB is challenging and we have developed necessary processes and trained our manufacturing partners to facilitate the same.
About the author

Ratheesh Nair is the Chief Technology Officer at C Electric Automotive Drives – an engineering company based out of Cochin with R&D focus on powertrains of light electric vehicles.
Subscribe today for free and stay on top of latest developments in EV domain.
According to certain informations, it is possible to use asynchronous AC Induction Motor with VFD along with Regenerative Module for utilising Brake Energy. This system is similar to that used for Elevators normally using asynchronous AC Induction Motors.
Will you or someone else throw some light on this and introduce a manufacturer capable of supplying such VFD. Best Regards.
H.K. Agarwal, Mob: +91 8826430489
symparhk@gmail.com
If only we can control the Kinetic Force of flywheel without causing any harm to the motor, whenever the vehicle slows down, then the problem will have been half solved.
Hi
I am in Ghana. I love electric vehicles and I have plans to go into it’s design and assembly locally instead of the diesel/petrol vehicles. How can you advise me?
Tom
Hello Thomas,
you can start reading research papers and use resources from various databases across internet. Try going for assembly first , buy/rent neeeded components and assemble them , further try retrofitting where you can get to know in detail about each component. Then you can design similarly on 3D modelling softwares and probably even sell/design for electric vehicle starups and companies. The needed necessary information can be found in vehicles dynamics books ( you can search for the names of the same) , youtube videos , research papers, articles , blogs etc.
Hoep it helped,
regards,
Vayu technologies
India
Pingback: Motor controller supplier C-Electric raises an undisclosed amount at a valuation of USD 4 million • EVreporter
Pingback: Gyrodrive Machineries, C Electric and Fashmo Energy, emerge winners at iCreate EVangelise’22 • EVreporter